Abstract
Background:
“Noise” can be defined as any unwanted sound. Soft drink plants, which produce the raw materials used in most carbonated beverage factories, are sources of noise.Objectives:
This study investigated the noise pollution present in a soft drink CO2 gas injection plant, in order to present noise control measures.Materials and Methods:
The instructions specified by the canadian center for occupational health and safety (CCOHS) were followed during the noise study, and a sound level meter, CEL.450 calibrated with CEL-110.2 based on ISO-9612 methods, was used to record the sound pressure level (SPL) at each grid point. SPL was determined in weighting scales A and C. and a noise survey map of equivalent SPLs was drawn for each part. Each part of the floor area of the soft drink factory where SPL exceeded 85 dBA was identified from the noise survey map to determine the causes of high levels of noise. In order to reduce noise level in each part, the absorption coefficient, transmission loss, and noise reduction rate were calculated in the proposed control area.Results:
According to the study results, noise levels in a CO2 plant’s house and control room ranged from 88 to 102 dB and 79 to 82 dB (A), respectively. In order to reduce the amount of emitted noise in the CO2 plant house and control room, a noise control plan was implemented in each part of the facility; it was met with effective results.Conclusions:
The findings of this investigation have clearly revealed that plant workers are at risk of developing noise-induced hearing loss. However, after the implementation of a noise control plan in each part of the facility, the noise dose received by workers has significantly decreased. The need to implement a noise conservation program was established<b>.</b>Keywords
1. Background
The gradual increase in undesirable and hazardous noise levels has perplexed our living and working environments; therefore, noise reduction is now a very important issue. Noise exposure is associated with a range of health effects (1). The world health organization estimates that about 278 million people worldwide have moderate to severe types of hearing loss (2). In fact, “noise” can be defined as any unsolicited or unwanted sound that is uncomfortable mentally or the cause of physiological and psychological tension (3, 4). Noise also has indirect effects on human performance, including efficiency and productivity reduction and the increased risk of accidents and errors due to decreased focus (5). Today, most noise problems in industrial environments are related to process equipment resources. From an industrial standpoint, the origin of noise from equipment is related to several factors, such as the structural and mechanical nature of devices, the amortization of mechanical parts, the improper functioning of machineries’ moving parts, the high-speed flow of fluids in canals, and the structural vibration of devices as a result of improper foundations (6, 7). In soft drink CO2 gas injection plants, special equipment, such as pumps, compressors, boilers, cooling towers, canals, gas and steam valves, and other vibrating equipment are considered to be the main sources of noise and vibration. Most noise pollution in this environment is related to the suction compressor (8). Kisku and Bhargava (9) determined main sources of noise-producing machines in a thermal power plant. Their results revealed that the lowest mean noise, 70.37 dB (A), was found in the control room, and the FD fan (forced draft fan) and compressor generator created the highest noise levels, 95.91 and 89.98 dB (A), respectively. Kerketta (10) reported on the noise levels of equipment furnaces, boilers, and cooling tower systems in a steel factory, noting that they range from 83 to 98 dB (A). In another study by Singh et al. (11) in a small-scale hand tools manufacturer in India, the results showed that noise levels were between 86.5 and 110 dBA. Kumar et al. (12) studied eight rice mills in India. Their results showed that noise levels were above 85 dBA, and the workers were exposed to high levels of noise. Oyedepo and Saadu (8) studied noise exposure in a variety of processing and manufacturing industries, and their results showed that noise control intervention had a significant impact on noise exposure levels in factories.
2. Objectives
This study aimed to investigate noise pollution and to implement a noise control plan for a soft drink CO2 gas injection plant.
3. Materials and Methods
The study was conducted in a soft drink plant during July and August 2015. The factory has three shifts (morning, evening, and night). The noise data were collected during all shifts. The mean relative humidity and mean temperature during the period of the survey in the factory’s ambient workspace were 68 ± 4.3% and 26 ± 3.2°C, respectively. The instructions of canadian center for occupational health and safety were followed during the noise study (13). Grid points were marked on the floor of the work area at a spacing interval of 1 m × 1 m. and noise pressure levels were measured in the center of each square. The sound pressure levels (SPL) around the suction compressor were measured at each defined station, characterized on the designed grid map, using sound level meter CEL.450 calibrated with CEL-110.2 and based on ISO-9612 and ISO-11200 methods (14). A sound level meter was held on a tripod 1.5 m above the floor, to prevent the shielding of noise by any reflector objects. The direction of the microphone was pointed towards the nearby noisy source. The noise spectrum and the sound pressure level in weighting scale “A” were recorded at each grid point for one minute. A noise map of equivalent noise levels was drawn for each part of the factory by drawing contour lines on the layout of the soft drink compartments among the points of equal sound pressure level. The distribution of the sound pressure level plan was established with the Sound PLAN software (15). The received noise doses were measured during each shift using noise dosimeter TES-1345 calibrated with CEL-282. In this way, the dosimeter was attached to the worker’s lumbar region, and its microphone was attached to the worker’s collar from the back region. The rate of the dose workers received during the three work shifts of morning, evening, and night were measured. The acoustic characteristics of rooms and the walls separating those rooms around the CO2 gas injection unit were reviewed based on noise transmission loss. Sound transmission loss calculated using following formula (16):

Where; f = frequency (Hz), W = surface density (kg/m2). The equation below was used to calculate sound transmission loss after implementation of the noise control plan in each part:

Where: SPLs = the average sound pressure level in the source area, SPLr = the average sound pressure level in the adjacent area, S = the surface area of the partition sq. m, A = the absorption, in sabins, in the adjacent area.
4. Results
The details of the soft drink factory’s equipment are presented in Table 1. It is also worth noting that the compressor for the factory’s CO2 machines was placed on a foundation of 0.8 m height. The materials used in the factory’s building are listed in Table 2. Thirteen male workers, spread across three shifts, were enrolled in the study. The mean age and the mean work experience for the men were 35 ± 8 and 19 ± 6 years, respectively. The results of the measurements of the SPL at the considered stations in the CO2 plant house, in the form of a contour noise map, are presented in Figure 1. The noise levels ranged from 88 to 98 dB (A), and the dominant frequency was 4,000 Hz. Near the sources of the sound, noise levels were from 95 to 98 dB (A). The evaluation results of the SPL at six stations around the suction machine, with noise frequency analyses and the SPL in a linear weighting (line) and A, were performed, and it was determined that workers are exposed to broadband noise in the soft drink factory. The overall noise level in the factory ranged between 88 and 99 dBA. Table 3 presents SPLs in the factory’s working zones. It can be seen that the workers nearest the CO2 compressor are exposed to higher levels of noise than those who work in other areas. Table 4 represented noise levels before and after noise control in two areas (the control room and the CO2 plant house). The results of noise measurements, taken in order to determine the total amount of workers’ exposure during the three shifts (morning, evening, and night) before and after intervention are shown in Table 5.
Details of Soft Drink Plant Area Considered for the Study
Noise Source (Machines) | Floor Space Occupied by Machinery m × m | Maintenance Status |
---|---|---|
Suction compressor | 5 × 3 | Poor |
Boiler burner | 6 × 4 | Good |
Cooling coils | 1.5 × 3 | Moderate |
Freon compressor | (3) 1.5 × 1.5 | Good |
Acoustic Materials Used for the Walls, Flooring, and Roof of the Soft Drink Factory
Area | Wall | Floor | Ceiling | Height of Wall, m |
---|---|---|---|---|
CO2 plant house | Painted bricks | concrete | Inclined with a gradient of 10%; cement sheeting with aluminum lining on the inside and a middle layer of fiberglass | 7 |
Control room | Painted plaster | mosaics | Painted plaster | 3.5 |
Noise Map Contours of the CO2 Plant House and Control Room
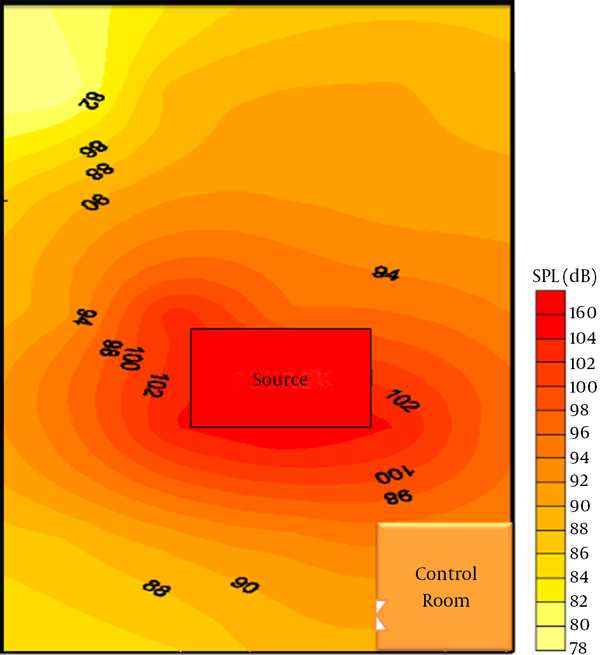
Sound Pressure Levels of the Soft Drink Factory in Workers’ Various Operating Zones
Work Zone | Number of Workers (Per Shift) | Sound Pressure Level | LAeq-8 Hours dB-A | TLV-ACGIH dB-A | |
---|---|---|---|---|---|
Minimum, dB-A | Maximum, dB-A | ||||
Near the suction compressor, at 1.5 meters | 2 | 90.8 | 98 | 93.7 | 85 |
Between the suction compressor and cooling coils | 2 | 91.4 | 99 | 94.9 | 85 |
Near the permanganate tank at 3 meters from suction compressor | 3 | 88.7 | 90.1 | 89.1 | |
Between the boiler burner and suction compressor (preparation of monoethanolamin) | 3 | 89.8 | 99.3 | 95.4 |
Results of Noise Reduction Plans in two Areas, Before and After the Implementation of the Noise Control Plan
Target | SPL Before Intervention dB | Control Intervention | Transmission Loss, dB | SPL After Intervention dB | |
---|---|---|---|---|---|
Theoretical | Actual | ||||
Control room | 81 | Replacement and installation of insulated steel doors with a thickness of 2 mm, UPVC windows with double-glazed glass | 34 | 25.5 | 55.5 |
CO2 plant house | 92.5 | Installation of porous polyurethane foam with a thickness of 2 inches as a noise absorber | 11.2 | 11 | 81.5 |
Dosimeter Results for the Three Shifts
5. Discussion
According to the study results, noise levels in the CO2 plant house and control room ranged from 88 to 102 dB and 79 to 82 dB (A), respectively. This finding is similar to the 2010 studies by Oyedepo and Saadu (8) and Ali (17). The employees in this industry commonly work at least eight h/day and six days/week (44 hours/week), all while being exposed to high noise levels above occupationally permissible limits (18, 19). Thus, in order to reduce the amount of emitted noise in the CO2 plant house and control room, a noise control plan was implemented in each area. The noise control plan considered factors such as cost, noise reduction efficiency, and applicability. The noise level in the control room before implementing the noise control plan was 81 dB. After applying the noise control plan, doors and windows were modified and replaced in the control room and, as a result, the noise level was reduced to 55.5 dB. Further, by installing sound-absorbing materials in the CO2 plant house, noise levels changed from 92.5 dB to 81.5 dB. The health and safety executive, in 2013 (20), and Oyedepo and Saadu (8), in 2010, reported similar results. Results of noise dosimetry before applying the noise control plan showed that all workers in the plant’s three shifts were exposed to high doses of noise. In this regard, the allowable working time was calculated to be only about three hours out of an eight-hour shift. After applying the noise control plan, the allowable working time was increased to about 5.5 hours. The findings of this study have clearly revealed that workers in the soft drink factory under investigation are at high risk of developing noise-induced hearing loss, thus an urgent reconsideration of noise levels and the use of hearing protection are essential, in addition to engineering control measures to mitigate such risks. In the present study, the results showed that, after implementation of a noise control plan in the CO2 plant house and control room, the noise levels received by workers decreased significantly. Moreover, workers’ allowable working time can be increased by using personal hearing protection by up to seven hours, in order to cover all of the time worked during a shift. Still, close attention to workers’ hearing protection and their health status and performance should not be forgotten.
Acknowledgements
References
-
1.
Chen S, Jiang Y, Chen J, Wang D. The Effects of Various Additive Components on the Sound Absorption Performances of Polyurethane Foams. Adv Mater Sci Eng. 2015;2015:1.
-
2.
Natalizia A, Casale M, Guglielmelli E, Rinaldi V, Bressi F, Salvinelli F. An overview of hearing impairment in older adults: perspectives for rehabilitation with hearing aids. Eur Rev Med Pharmacol Sci. 2010;14(3):223-9. [PubMed ID: 20391963].
-
3.
Kam PC, Kam AC, Thompson JF. Noise pollution in the anaesthetic and intensive care environment. Anaesthesia. 1994;49(11):982-6. [PubMed ID: 7802247].
-
4.
Schnelle JF, Alessi CA, Al-Samarrai NR, Fricker RJ, Ouslander JG. The nursing home at night: effects of an intervention on noise, light, and sleep. J Am Geriatr Soc. 1999;47(4):430-8. [PubMed ID: 10203118].
-
5.
Haines MM, Stansfeld SA, Job RF, Berglund B, Head J. Chronic aircraft noise exposure, stress responses, mental health and cognitive performance in school children. Psychol Med. 2001;31(2):265-77. [PubMed ID: 11232914].
-
6.
Duijm NJ, Fievez C, Gerbec M, Hauptmanns U, Konstandinidou M. Management of health, safety and environment in process industry. Saf Sci. 2008;46(6):908-20.
-
7.
Bell LH, Bell DH. Industrial Noise Control:Fundamentals and Application. 2 ed. New York: Marcel Dekker; 1994.
-
8.
Oyedepo OS, Saadu AA. Assessment of noise level in sundry processing and manufacturing industries in Ilorin metropolis, Nigeria. Environ Monit Assess. 2010;162(1-4):453-64. [PubMed ID: 19274486]. https://doi.org/10.1007/s10661-009-0809-9.
-
9.
Kisku GC, Bhargava SK. Assessment of noise level of a medium scale thermal power plant. Indian J Occup Environ Med. 2006;10(3):133-9.
-
10.
Kerketta S, Dash PK, Narayan LT. Work zone noise levels at Aarti steel plant, Orissa and its attenuation in far field. J Environ Biol. 2009;30(5 Suppl):903-8. [PubMed ID: 20143727].
-
11.
Singh LP, Bhardwaj A, Deepak KK, Bedi R. Occupational noise exposure in small scale hand tools manufacturing (forging) industry (SSI) in Northern India. Ind Health. 2009;47(4):423-30.
-
12.
Kumar GVP, Dewangan KN, Sarkar A, Kumari A, Kar B. Occupational noise in rice mills. Noise and Health. 2008;10(39):55-67.
-
13.
Bank HSD. Canadian Centre for Occupational Health and Safety. Canada: Q-1; 1998.
-
14.
ISO. Acoustics, Determination of occupational noise exposure engineering method, Engineering method.ISO 9612. Switzerland: International Organization for Standardization; 2009.
-
15.
Software G. Surfer(R) Version 8.0 ReadMe File. Version 8.0 ed. 2002.
-
16.
Randall FB. Industrial noise control and Acoustics. New York: Marcel Dekker Inc; 2001.
-
17.
Ali SA. Industrial noise levels and annoyance in Egypt. Applied acoustics. 2011;72(4):221-5.
-
18.
Atmaca E, Peker I, Altin A. Industrial noise and its effects on humans. Pol J Environ Stud. 2005;14(6):721-6.
-
19.
Zeng L, Cai DL, Hou XA, Sun JY, Li HJ, Lv JQ, et al. Personal noise exposure of overhead-traveling crane drivers in a hot rolling mill. Chinese J Ind Med. 2007;20(1):33.
-
20.
Health and Safety. HSE, Sound solutions for the food and drink industries. Health and Safety; 2013. Available from: www.hse.gov.uk/pubns/books/hsg232.