Abstract
Background:
One of the most common harmful factors in the workplace is noise. Noise control is a factor beneficial for health and safety in the workplace.Objectives:
The current study aimed to design and manufacture a silencer for the cooling tower pump of Sarcheshmeh Copper power station in order to control noise.Methods:
In this study, sound pressure level was measured by the use of a sound level meter (B & K 2260). Measurement was carried out in the light of ISO 1996 standard. After studying technical and acoustic features of the noise source, a dispersive-absorptive silencer was designed to control noise pollution generated by the cooling tower pump of the thermal station. After analyzing the frequencies of sound pressure level and using available data, a cylindrical silencer (with a diameter of 1.5 m and height of 3 m) was designed and manufactured. The internal part of the silencer was filled with different columns of absorbent material covered with punched metal. Therefore, the silencer consisted of (1) acoustic diffuser, (2) acoustic chamber, and (3) acoustic channels.Results:
Measurements showed that, at a distance of 1 m from the source, sound pressure level reduced from 127 dBA before installing the silencer to 79 dBA after the installation, resulting in a reduction of 48 dBA.Conclusions:
Using a silencer with absorbent material (glass wool) is very effective in reducing the noise generated by the pump.Keywords
1. Background
One of the common harmful factors in the workplace is noise (1-3). Intense noise in workplaces is one of the most serious problems around the world. For example, over 30 million workers in the US are exposed to dangerous noises (4, 5). In addition, around 4 to 5 million German workers (constituting 12% - 14% of the workforce in Germany) are exposed to unauthorized noise. Over the past ten years, the proportion of the population exposed to environmental noises higher than 65 dB has increased from 15% to 26% (6). Noise-induced hearing loss is affected by sound intensity, sound frequency, and individual’s sensitivity (7). According to different reports, the noise-induced damage is among the top ten harmful factors. The results of the previous research show that, in the US alone, 7.4 to 10.2 million industrial workers are at the risk of noise-induced hearing loss (1). There are different procedures to control and prevent noise pollution in industry. The use of each procedure is a function of the type of sound source, physical conditions, and the purpose of noise control. In most of the industries, transferring air or gas from one part to another causes a lot of noise. In order to reduce the noise pollution, some particular instruments, known as sound reduction tools or acoustic filters, are used. An acoustic filter or silencer is an instrument that prevents the transmission of sound waves without significantly obstructing the passage of air or gas (8). Silencers, which are used to reduce the noise of air outputs, channels, and fans (9), are divided into three general groups: reactive, absorptive, and dispersive. In its simplest form, a reactive silencer consists of an expansion chamber, which is installed somewhere in the channel that transmits sound. Impedance changes in the place where the cross-sectional area of the channel changes can cause sound wave reflection. This reflection is combined with the secondary destructive interference of the incoming sound wave, hence attenuating the noise through the channel. Absorptive silencers contain some fibrous or porous materials, which absorb the sound transmitted through the machine. One of the simplest forms of absorptive silencers is a channel covered with absorptive materials. In order to have a silencer of arbitrary length, the internal walls of a conduit can be covered with an absorptive material (9, 10). Dispersive silencers are in fact pressure relief devices that are installed somewhere throughout the stream to diffuse high-velocity gas flow into smaller lower-velocity streams. Noise is significantly reduced because of this process. These machines can be made in the form of a cage and installed beyond valves or at the control valves (11).
2. Objectives
Given the importance of noise control in occupational health engineering, the following objectives were pursued in this study:
(1) Designing and manufacturing a silencer for the cooling tower pump of Sarcheshmeh Copper power station in order to control noise
(2) Minimizing the noise generated by the power station pump by simultaneously installing a silencer and using absorptive materials in the cooling tower pump
(3) Comparing the noise generated by the cooling tower pump before and after the installation of the silencer and absorptive materials and comparing the results with the standard sound pressure level
3. Methods
This study, which was conducted in 2015, was an attempt to investigate how noise could be controlled in Sarcheshmeh Copper complex. The main objective was to design and manufacture a silencer for the cooling tower pump of the thermal power station.
Technical and acoustic properties of noise sources were initially identified. Then, a plan was presented to design, manufacture, and install a silencer for the cooling tower pump of the thermal power station.
3.1. Investigating Features and Properties of Noise Sources
3.1.1. Technical Properties of the Noise Sources
One of the main issues in designing silencers is identifying the sources of noise. Therefore, after an initial investigation, the following sources were identified as the main noise generating factors in the outlet of cooling tower pump:
(1) The valve that vents out the stem; (2) pressure difference before and after the valve, which generates noise within the valve; (3) high velocity of the steam that passes through the pipe outlet.
3.1.2. Acoustic Properties of the Noise Sources
In order to study the features of the noise generated by the outlet of the cooling tower pump, the sound pressure level was measured at different octave frequency bands based on the dBA weighting chart ranging from 31.5 to 8000 Hz. The measurement was conducted by the use of a sound level meter (B & K 2260). Sound power level (SWL) at a particular distance (R) from the source was calculated through the following formula (12):
SWL = SPL + 20 Log R - 11
Where
SWL: sound power level (dB)
SPL: sound pressure level (dB)
R: distance from the noise source (m)
After calculating SWL for each frequency band, the total noise of the source was calculated through the following equation (13):

After conducting all necessary calculations, SWL for the outlet of the cooling tower pump was found to be 135 dBA. The level of noise varies at different distances from the source.
3.1.3. Measurement
In the present study, noise measurement was conducted by the use of a sound level meter (B & K 2260). Measurement was carried out in the light of ISO 1996 standard. In order to enhance measurement reliability, the sound level meter was calibrated by a calibrator before each new measurement.
3.2. Designing, Manufacturing, and Installing Silencers
3.2.1. Limitations in Designing Noise-Controlling System
Since steam is emitted from a small cross section into the air with high velocity, attempts to prevent or constrain the emission of steam cause reverse pressure or severe blow to the system due to steam return. This may lead to a lot of damage. Thus, the major issue is creating no blockage in the free flow of steam. Diverting the path of the existing steam or creating winding paths may causes a blow to the system and eventually leads to damages. Consequently, we need to use direct paths in designing the system as much as possible. Another limitation is that the steam emitted from the outlet has a temperature over 162 °C. Hence, the materials that are used in the noise controlling system should be able to tolerate this high temperature and humidity.
3.2.2. Designing
Identifying the acoustic features of the noise source is the first step in designing instruments for controlling noise pollution. Knowing the acoustic features and physical characteristics (e.g. location, operational procedure, and limitations) of the noise source can help us design a noise control system with maximum efficiency. It should be noted that, in controlling and reducing noise pollution, there is no limitation for noise reduction, and various procedures can be used to reduce the amount of noise significantly. However, greater reduction in sound pressure level increases the costs of implementing noise control procedures. Therefore, the financial aspect is another factor that must be taken into account in designing noise-controlling systems. The proposed standards have presented a range of acceptable noise for occupational exposure. Thus, it is not advisable to spend more money to reduce noise to a level below the proposed standards. Some other important factors in designing the silencer are its location, its safety (i.e. making sure that the silencer will not fall over during the operation), and ease of installation.
In order to reduce and control the generated noise in the outlet of the vent of the cooling tower pump, the following three steps must be taken: (1) reducing air velocity; (2) absorbing the generated noise as the steam passes through the vent; and (3) preventing the noise regeneration. To reduce air velocity in the designed silencer, we should decrease the cross sectional area of the outlet pipe. Based on the following equation, the larger the difference in the cross sectional areas of the air passage, the lower the air velocity (8).
V2 = V1S1/S2
Where
V2: final velocity of air front (m/s)
V1: initial velocity of air front (m/s)
S2: final cross section area (m2)
S1: initial cross section area (m2)
As air passes from S1 to S2, it produces a lot of noise. In order to absorb this generated noise, suitable absorbents should be used throughout the air passage. In order to avoid noise regeneration in the designed silencer, the surface of the silencer must be resistant to air passage. Furthermore, the air passage should be designed to absorb the maximum amount of noise and the absorbents exert the minimum amount of mechanical resistance.
The generated noise in the vent outlet of the cooling tower pump is due to the high velocity of the air that passes through, a phenomenon known as jet noise. In this phenomenon, high-velocity air molecules collide with the ones in the surrounding environment (which is almost static), hence producing a noise of 135 dBA at the source and 127 dBA a meter from the vent outlet. Measurements indicate that sound pressure level at ground level is 125 dB. In order to have a noise of 85 dBA, we should reduce the noise level by 40 dBA. Given that the volume of the vented air is fixed, air velocity can decrease by raising the cross section area. To reduce air velocity, we need to use a silencer that is both absorptive and dispersive. Therefore, in this project, the designed silencer should not only absorb the noise generated by air passage, but also reduce its velocity so that the ventilation would happen in low speed. Some other parameters that are important in designing a silencer are: (1) flow of exhaust air; (2) cross sectional area; and (3) frequency band of the sound pressure level (8).
4. Results
4.1. Measuring Sound Pressure Level Before and After Installing the Silencer on the Outlet of the Cooling Tower Pump
Figure 1 represents the results of measuring sound pressure level before and after installing the silencer on the outlet of the cooling tower pump of Sarcheshmeh Copper power station in various frequencies ranging from 31.5 Hz to 8000 Hz.
The Results of Measuring Sound Pressure Level Before and after Installing the Silencer on the Outlet of the Cooling Tower Pump
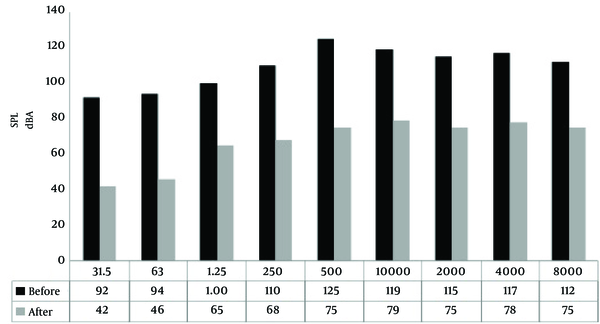
4.2. The Results of Design Calculations
The steam that passes through the vent outlet has a temperature of about 162°C and a pressure of 530 kg/m2. Thus, we cannot use only acoustic materials for reducing noise because to achieve the target degree of noise reduction, a large amount of acoustic materials should be used. When steam passes through all these materials, a large volume of water is produced, which reduces the efficiency of the silencer. As a result, we need to use diffusers and a small amount of acoustic materials that do not absorb water. A normal diffuser reduces noise level by 25 to 34 dB. Therefore, on average, a diffuser reduces noise level by 30 dB. Hence, the sound pressure level must decline by10 dB through using acoustic panels. The following formula illustrates the degree of noise reduction by the silencer (8):
TL = 4.2A × 1.4 × LH/4h
A: the absorbent coefficient of acoustic material (m2 or sabin)
L: silencer length (m)
H: silencer width or diameter (m)
H: distance between columns of absorbent material (m)
Therefore, the degree of noise reduced by the silencer is equal to:
TL = (4.2) × (0.7) × 1.4 × 2 × 1.5/4 × 0.15 = 13 dB
On the one hand, the passage of air through acoustic panels’ chamber causes reduction in noise. On the other hand, the installation of two chambers (one after the noise diffuser and one before the place where air enters acoustic panels) further reduces the noise. If we consider the diameter of the present outlet pipe as 10 inches (25 cm), its cross sectional area will be 500 cm × 2. However, in the silencer (with a diameter of 1.5 m and the use of 75 cm of absorbent materials), the cross sectional area of the air outlet is equal to 88,000 cm × 2, which is 16.7 times greater than the cross sectional area of the inlet. Thus, the noise generated in the steam outlet almost fades. Since the first sound energy peak occurs in the one fourth of the wavelength, the minimum thickness of the acoustic materials that are used to absorb a noise with a given wavelength should be equal to λ/4. The following formula is used for the frequency of 1000 Hz:
λ = c/f = 0.35 m
Where
(m) Wavelength: λ
C: Sound speed (m/s)
F: Frequency (Hz)
The average wavelength is 35 cm. The thickness of the acoustic panel should not be less than λ/4, which is equal to 0.087 m. Thus, in the designed silencer, we included 7 columns of absorbent materials in which, the diameter of the acoustic panels was 12 cm. Therefore, it is predicted that the installation of this silencer will result in a noise reduction of 35 -40 dB. In total, the designed silencer had a diameter of 1.5 m, a height of 3 m, and 7 columns of absorbent materials with a height of 2 m and a thickness of 12 cm. Moreover, the silencer had a noise diffuser with a height of 35 cm located in the inlet. The space between the noise diffuser and the inlet of acoustic absorbents in the silencer had a height of 65 cm in order to diffuse noise and uniform air stream. As noise enters this chamber, it diffuses and uniformly spreads through the absorbent passages.
4.3. Selecting Materials
In order to prevent the destruction of absorbent materials, punched sheets were used to cover them. These sheets should have more than 50% of empty space over their surface. Therefore, the used sheets were 2 mm thick and their holes had a diameter of 5 mm. These sheets protect absorbent materials against air velocity. On the other hand, they let sound waves enter the chamber and prevent the exit of the proportion of sound waves that have not been absorbed. In selecting the materials for manufacturing the silencer, we needed to consider three factors: efficiency, safety, and low cost. Because steam passes through the vent, galvanized and steel punched and outer sheets were used. If the outer sheets are thick enough, they will prevent noise leakage. The increase in the density and thickness of absorbent materials enhances their efficiency. It should be noted that if absorbent materials are too dense, they could not absorb high frequency noises. This is because high frequency noises cannot penetrate materials with very high density, hence reduction in noise absorption. The used absorbent should be porous so that sound waves can enter. Furthermore, the density of the absorbent is effective in noise absorption. For the purpose of this study, the best absorbent was glass wool with a density of 100 kg/m3. It should be noted that absorbent materials alone could not appropriately prevent the passage of noise. Nonetheless, if they are put between two metal layers, sound can be converted into heat and will be absorbed in frequent reflections. The higher the density and the thickness of the used metal, the better its performance in reducing noise (8).
4.4. Manufacturing and Installing the Silencer
After selecting the required materials and determining the sizes of the silencer, the designed plan was given to the manufacturing team, which manufactured two silencers accordingly. These silencers were installed in the predetermined areas. Figures 2 and 3 show the place where the silencers were installed.
Silencers
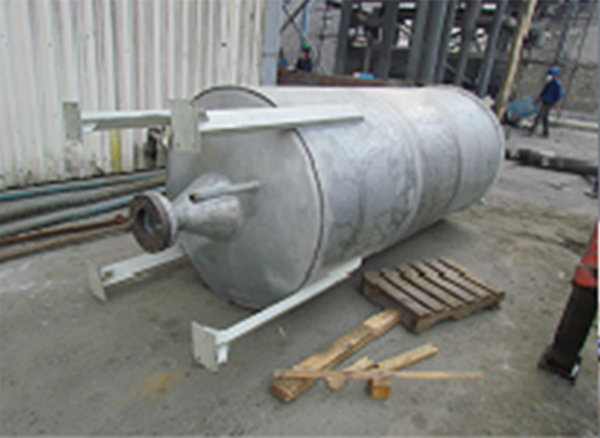
Silencers
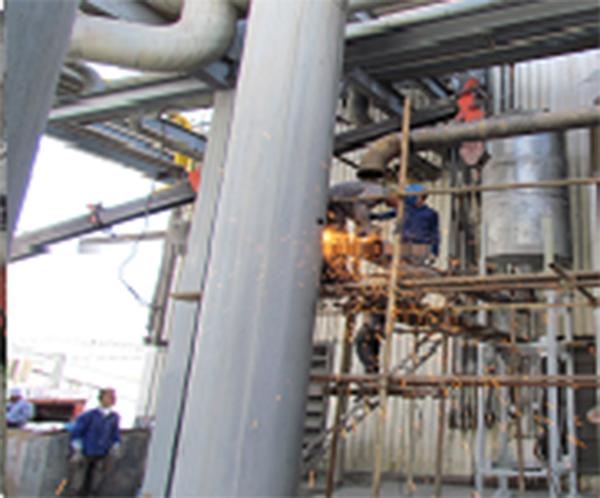
In order to remove humidity and prevent water from entering the silencer (hence reducing silencer efficiency), a discharge pipe was installed in the silencer inlet for drainage purposes (Figure 4). Figure 5 shows the final position of the installed silencer.
Silencer Inlet
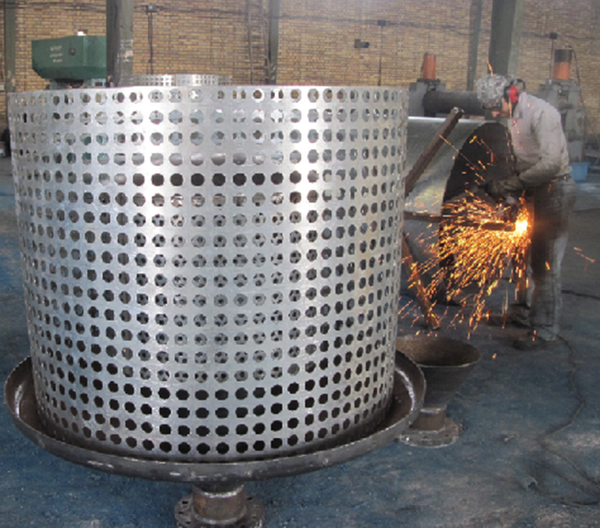
The Final Position
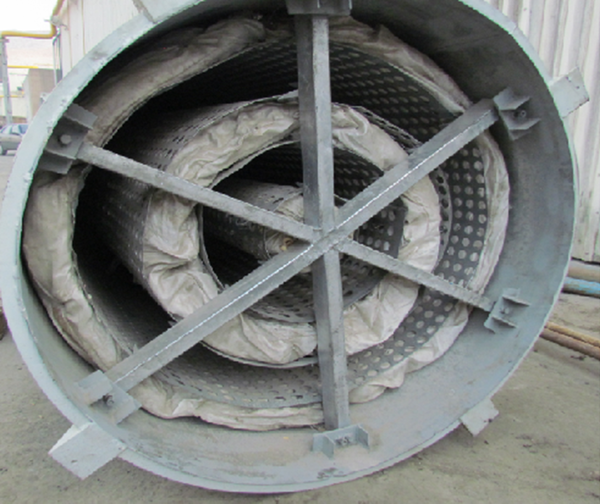
5. Discussion
This study, which was conducted in 2015, aimed to design and manufacture a silencer for the cooling tower pump of Sarcheshmeh Copper power station in order to control noise.
As indicated in Figure 1, noise level measurement ranged from 21.5 Hz to 8000 Hz. The results of measurements showed that the highest sound pressure level was registered at frequencies of 500 to 4000 Hz.
According to the obtained results, the highest sound pressure level was measured before installing the silencer on the outlet of cooling tower pump. It was 125 dB at the frequency of 500 Hz. Measuring sound pressure level after installing the silencer demonstrated a significant decline. More precisely, after installing the silencer, sound pressure level declined by 40 dB at the frequency of 500 Hz. The degrees of noise reduction after installing the silencer were 50 dB, 40 dB, and 39 dB at frequencies of 500 Hz, 2000 Hz, and 4000 Hz, respectively. Therefore, the silencer and the used absorbent materials were efficient. In a laboratory study, Selamet et al. (2003) investigated the effect of silencers filled with string fibers on reducing noise. They found that absorbent materials increase the degree of noise reduction. Furthermore, the rise in the thickness of absorbent materials leads to a decline in the number of peaks and causes some changes in the transmission loss peak frequency (14). Lancaster et al. (2007) studied the impact of microfiber cloth on absorbing noise and concluded that the density of microfiber cloth plays a more important role than its thickness and weight in reducing noise (15). We found that silencers with higher density are better noise absorbents, a finding that is in line with the results of previous studies. Wang et al. (2011) discovered that absorbent materials reduce transmission loss at resonant frequencies. They also found that absorbent materials with higher density are more efficient in absorbing noise. The results of studying dispersive silencers also indicated that higher density of absorbent materials decreases resonant frequency and increases transmission loss (16). Faezian et al. (2005) used numerical analysis to study factors that affect the performance of silencers. They found that using noise absorbents increases depreciation and removes transmission loss. Furthermore, they discovered that changing the density of absorbent materials enhances depreciation to a particular degree (17). Koizumi et al. (2002) demonstrated that as the density of absorbent materials increases, the sound absorption coefficient in the midrange and high frequencies goes up (18). Seddeq (2009) investigated the influence of various factors related to fiber materials on sound absorption coefficient. He concluded that absorbent materials with lower densities are more efficient in frequencies under 500 Hz, whereas absorbents with higher densities perform better in frequencies above 2000 Hz (19).
5.1. Conclusions
The most effective and useful procedure for reducing and controlling noise pollution is controlling noise at its source. The objective of the present study was to reduce the noise generated by the outlet of the cooling tower pump of the thermal station by at least 40 dB. Measurements were conducted before and after the installation of the silencers so that comparison was possible. The results indicated that, after installing the silencers, sound pressure level declined by 42 dB. According to the proposed standards, occupational exposure to noise in an eight-hour shift should be equal to 85 dB. Therefore, the staff will experience a noise below the standard level after installing the silencers. Noise level significantly decreased after installing the silencer and using absorbent material (glass wool). Thus, performing such projects not only is economical for every company/organization, but also improves the production efficiency and reduces financial costs of hearing loss among industrial workers.
It should be noted that, in this project, the silencer was manufactured based on Iranian technology. Thus, it was less expensive and more economical compared to silencers imported from other countries.
Acknowledgements
References
-
1.
Nassiri P, Zare S, Monazzam MR, Pourbakht A, Azam K, Golmohammadi T. Modeling signal-to-noise ratio of otoacoustic emissions in workers exposed to different industrial noise levels. Noise Health. 2016;18(85):391-8. [PubMed ID: 27991472]. https://doi.org/10.4103/1463-1741.195808.
-
2.
Nassiri P, Zare S, Monazzam MR, Pourbakht A. A Model to Determine the Level of Serum Aldosterone in the Workers Attributed to the Combined Effects of Sound Pressure Level, Exposure Time and Serum Potassium Level: A Field-Based Study. Jundishapur J Health Sci. 2016;9(2). https://doi.org/10.5812/jjhs-38167.
-
3.
Zare S, Nassiri P, Monazzam MR, Pourbakht A, Azam K, Golmohammadi T. Evaluation of the effects of occupational noise exposure on serum aldosterone and potassium among industrial workers. Noise Health. 2016;18(80):1-6. [PubMed ID: 26780955]. https://doi.org/10.4103/1463-1741.174358.
-
4.
Zare S, Nassiri P, Monazzam MR, Pourbakht A, Azam K, Golmohammadi T. Evaluation of Distortion Product Otoacoustic Emissions (DPOAEs) among workers at an Industrial Company exposed to different industrial noise levels in 2014. Electron phys. 2015;7(3):1126.
-
5.
Alimohamadi I. Occupational Noise. Iran Occup Health. 2006;3(1):1-3.
-
6.
Lercher P. Environmental noise and health: An integrated research perspective. Environ Int. 1996;22(1):117-29. https://doi.org/10.1016/0160-4120(95)00109-3.
-
7.
Clark WW. Hearing: the effects of noise. Otolaryngol Head Neck Surg. 1992;106(6):669-76. [PubMed ID: 1608632]. https://doi.org/10.1177/019459989210600610.
-
8.
Barron RF. Industrial noise control and acoustics. CRC Press; 2002.
-
9.
Randall FB. Industrial noise control and acoustics. Louisiana: Louisiana Tech Universitz Ruston; 2001.
-
10.
Bell LH. Industrial noise control. Marcel Dekker Inc; 1982.
-
11.
Harris DA. Noise control manual. Van Nostrand Reinhold; 1991.
-
12.
Foreman J. Sound analysis and noise control. Springer Science & Business Media; 2012.
-
13.
Beranek LL, Ver IL. Noise and vibration control engineering-principles and applications. John Wiley & Sons; 1992.
-
14.
Selamet A, Lee IJ, Huff NT. Acoustic attenuation of hybrid silencers. J Sound Vibrat. 2003;262(3):509-27.
-
15.
Na Y, Lancaster J, Casali J, Cho G. Sound Absorption Coefficients of Micro-fiber Fabrics by Reverberation Room Method. Textile Res J. 2016;77(5):330-5. https://doi.org/10.1177/0040517507078743.
-
16.
Wang CN, Torng JH. Experimental study of the absorption characteristics of some porous fibrous materials. Appl Acoustics. 2001;62(4):447-59. https://doi.org/10.1016/s0003-682x(00)00043-8.
-
17.
Faezian A, Razavi MRM, Onorati A. N-Junction Modeling in Perforate Silencers for Internal Combustion Engines. Scientia Iranica. 2005;12(4):348-58.
-
18.
Koizumi T, Tsujiuchi N, Adachi A. The development of sound absorbing materials using natural bamboo fibers. WIT Transactions Built Environ. 2002;59.
-
19.
Seddeq HS. Factors influencing acoustic performance of sound absorptive materials. Aust J Basic Appl Sci. 2009;3(4):4610-7.
reply